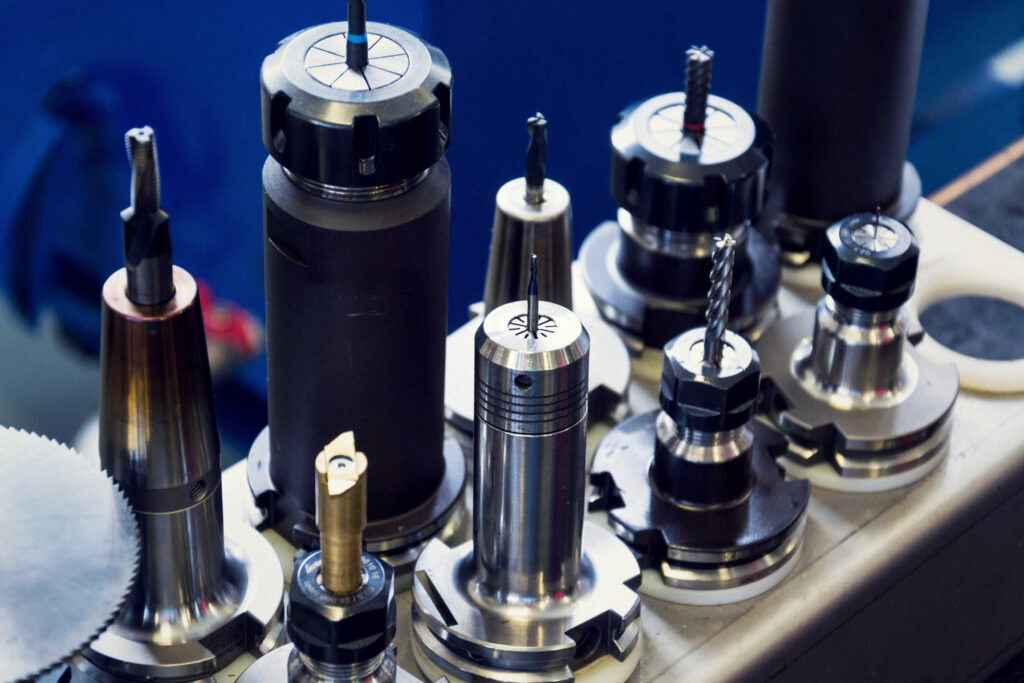
Cutting Tools: Types, Use Cases & Maintenance
“Which is the right tool for me?”
This question is top of mind for many professionals in manufacturing and machining industries, workshop owners, and hobbyists. Your project’s success depends on picking the right tool that:
- Ensures precision, efficiency, and longevity, while
- Minimising material waste and operational costs.
At Kota Cutting Tools, we understand this struggle. Therefore, this detailed piece will cover everything about different cutting tools, their specific uses, and the best ways to maintain their optimal performance.
What Are Cutting Tools?
Cutting tools are wedge-shaped, sharp-edged tools that remove extra layers through shearing action(s) [1]. This is to achieve a specific shape, size, and accuracy of the material. You’ll find these tools in many forms – from basic hand tools to advanced machine-controlled systems.
Classifications of Cutting Tools
These tools can be grouped into three main categories based on their cutting edges:
1. Single-Point Tools
Used in turning, shaping, and milling operations with one main cutting edge [2]. For Example, tools used in lathes, planers, shapers, and boring machines.
Suitable for:
- Precision turning and shaping operations.
- Producing complex profiles in a simple pass.
|
|
2. Double-Point Tools
Common in drilling operations [3], featuring two simultaneous cutting edges. Do note that conventional metal cutting drills have only two flutes. For example, twist drills, step drills, and center drills.
Suitable for:
- Creating precise holes in various materials.
- Applications requiring balanced cutting force distribution.
|
|
3. Multi-Point Tools
These tools contain more than two cutting points (ranging from three to 100 points), making it suitable for complex cutting patterns [4]. For example, milling cutters, grinding wheels, drills, reamers, broaches, and hones.
Suitable for:
- High-speed machining and precision cutting.
- Applications requiring multiple edges for efficiency.
|
|
Not sure which is the best choice for your project? Contact our team today for tailored recommendations! You can also visit our physical store in Puchong, Selangor.
Types of Cutting Tools
Cutting tools come in various forms, each designed for specific machining operations. Below are some key categories:
Milling and Slotting Tools
These tools are used to shape and cut materials in milling operations, allowing for precision machining of slots, contours, and surfaces.
- End Mills – Used in milling operations to create slots, pockets, and contours.
- Slitting Saws – Thin circular blades used for precision slitting and cutting.
- Tool Bits – Single-point tools used in lathe operations for shaping materials.
- Shank and Milling Cutters – Versatile tools for machining flat and contoured surfaces.
Hole-Making Tools
Designed to create, enlarge, or refine holes with precision, these tools ensure accurate dimensions and smooth finishes.
- Countersinks and Counterbores – Create recesses for screws and bolts.
- Drills – Used to create round holes in materials.
- Reamers– Enhance hole accuracy and improve surface finish.
- Rotary Burrs – Small cutting tools used for deburring and material removal.
Threading Tools
These tools are essential for creating internal and external threads, ensuring secure fastening and assembly.
- Hand Taps – Used for manually cutting internal threads.
- Machine Taps – Designed for high-speed thread cutting in automated machines.
- Threading Dies – Used to cut external threads on rods and fasteners.
Premium Quality Cutting Tools at Competitive Prices
Our cutting tools are expertly manufactured and rigorously tested to enhance machining performance and operational savings.
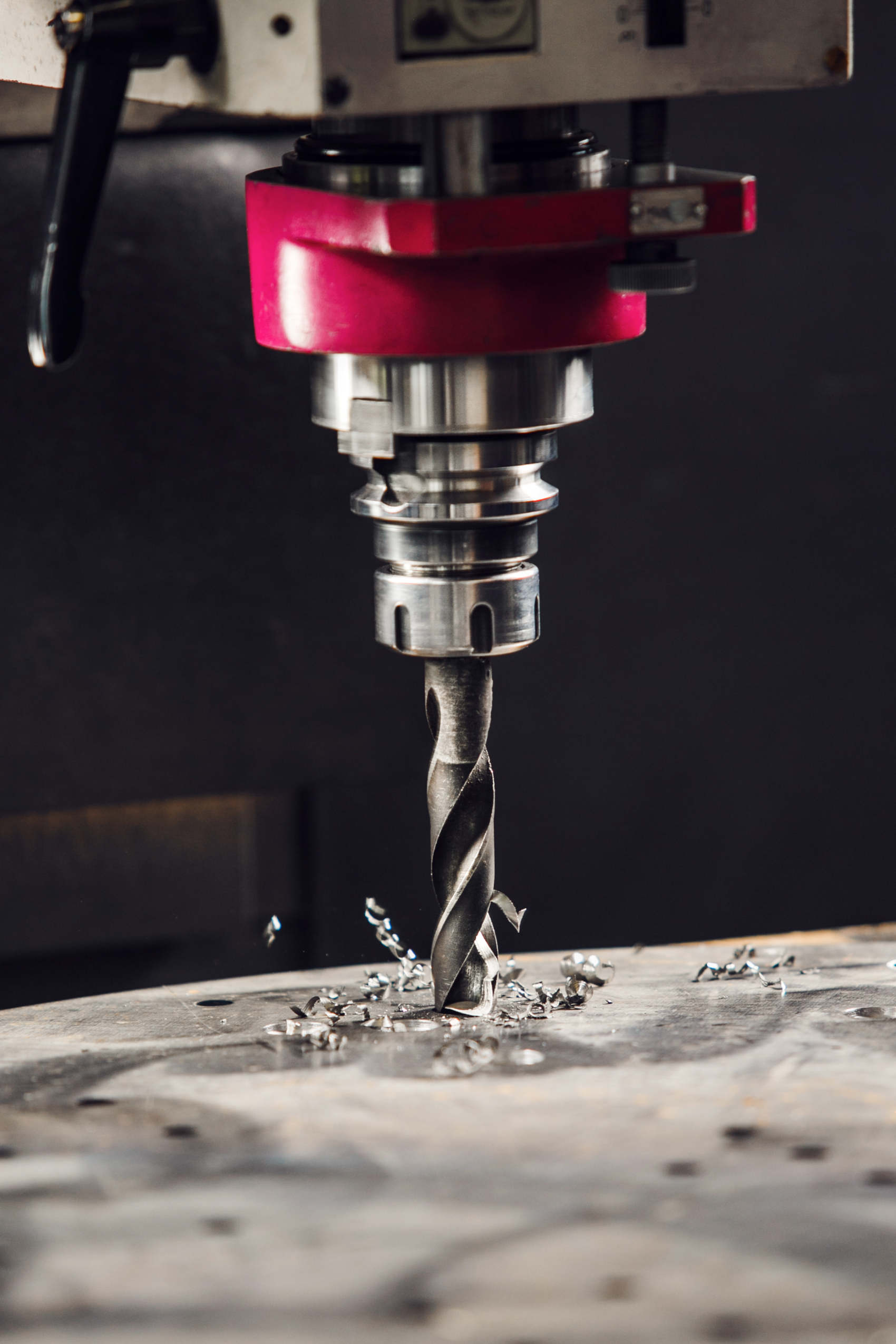
How to Make Your Tools Last Longer
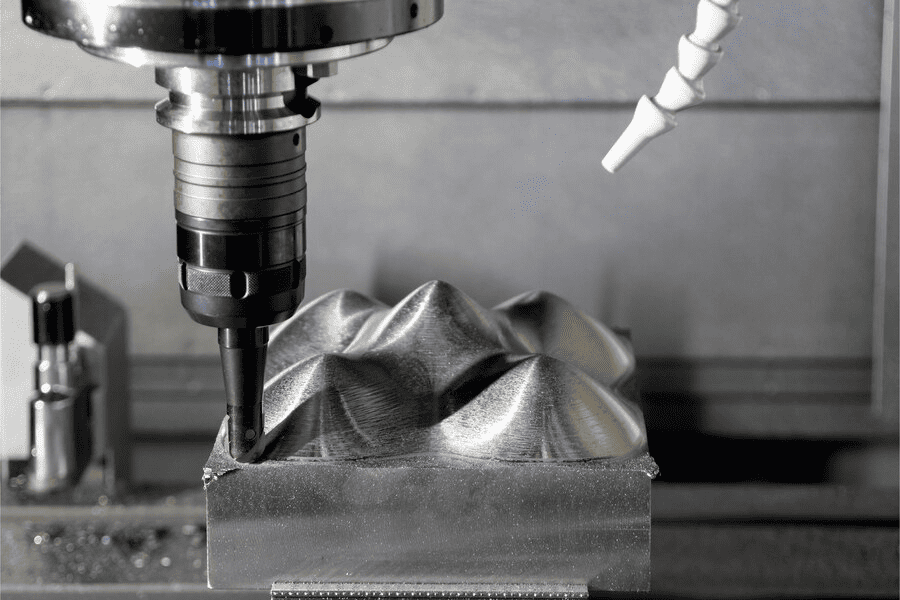
Photo by Freepik
The life of cutting tools depends on how well you maintain and store them. Research shows that most tools get replaced too early, and users only utilize 50-80% of their expected life [5].
1. Practice Proper Tool Storage Care
Carbide tools need separate storage in wood or plastic cases to avoid chipping when they touch other tools. A well-laid-out tool board makes selection easy and storage safe while boosting efficiency.
Tools stay in better shape when kept in a clean, dry space. A good cleaning before storage removes chips and debris that build up during machining.
2. Create a Regular Maintenance Schedule
Tool maintenance works best with consistent inspection and cleaning routines. Clean your tools after each use and look for wear or damage.
Good quality coolants help tools last longer by cutting down heat and friction during operation.
Tool monitoring systems can track wear patterns and spot potential failures before unexpected breakdowns happen.
3. Look Out For Signs of Tool Wear
Look out for these key wear signs:
- Flank wear runs parallel to cutting edges from abrasion
- Crater wear shows up on the rake face due to chemical reactions
- Thermal cracks run perpendicular to cutting edges
- Plastic deformation occurs when the cutting temperature gets too high for the grade
Tools need replacement if they show too much local damage or start making poor-quality parts. Chipping shows up as nicked or flaked edges and usually means the tool handled too much load during use.
Using proper cooling techniques and keeping an eye on cutting forces can make tools last a lot longer.
How Do I Choose the Right Tool?
Choosing the right cutting tools requires considering several factors that impact machining performance [6]. Before deciding, ask yourself:
What Materials Am I Cutting?
The workpiece material’s properties drive tool selection. Tools with better wear resistance and durability work best with harder materials.
The material’s toughness and ductility play a key role in tool choice. Materials that show high ductility need tools that keep their sharp cutting edges. We also need to review work-hardening characteristics since some materials get harder and tougher to cut during machining.
What Are the Project Requirements?
Tool selection criteria depend on component specs and machining conditions. Surface finish needs can range from rough textures to mirror-like finishes.
Tool choice changes with tolerance specs – precise machining capabilities are needed for tighter tolerances. The machining environment affects tool performance significantly through temperature, humidity, and dust levels.
What’s My Budget Like?
Tooling represents only 2% of the total cost, yet it affects productivity significantly [7]. Experts recommend not to confuse price with cost — don’t look at the prices of the cutting tools, look at factors such as metal removal rate which contribute to reducing overall cost.
Key selection factors include:
- Cutting speed abilities and feed rate needs
- Tool coating type and material grade match
- Machine tool abilities and power needs
- Production volume and batch size
Machining operations succeed when tools strike the right balance between performance and cost. High-quality cutting tools cost more but prove their worth through better output and less downtime.
In spite of that, the choice must line up with specific production needs and available machining capabilities.
Get Precision Cutting Tools at the Best Prices – Kota Cutting Tools
Cutting tools play a vital role in manufacturing and fabrication. Each tool has unique features designed for specific materials and applications.
You can maximize efficiency and achieve project success by knowing these characteristics.
As we mentioned earlier, one thing’s for sure: Premium tools may cost more upfront, but they deliver better results and last longer when maintained and stored properly.
With over 20 years of industry experience, Kota Cutting Tools is a leading cutting tools manufacturer in Malaysia that offers a complete range of cutting tools at competitive prices.
We ship locally and internationally. Our tool catalog carries renowned brands such as Volkel, V-Coil, Vergnano, Widia, IIDA Iron Works, WIS, KCT, SOMTA, and BELLOTA.
Need expert guidance or looking for the right tools? Contact our team today. You can also reach us at 03-8061 3671 or kotakctpuchong@gmail.com.
FAQ
What impacts the lifespan of cutting tools?
Cutting tool life is influenced by factors like cutting speed, feed rate, depth of cut, tool geometry, material type, work material, cutting conditions, machine rigidity, and the use of cutting fluids.
What materials are cutting tools made of?
Cutting tools are typically made from high-speed steel (HSS), carbide, ceramic, or cermet, depending on the application and material being cut.
What are the main categories of cutting tools?
Cutting tools are divided into three main types:
- Single-point tools – Used for turning and shaping.
- Double-point tools – Primarily for drilling.
- Multi-point tools – Include milling cutters and grinding wheels for complex cuts.
How can I extend the lifespan of my cutting tools?
To prolong tool life, store them in clean, dry conditions, preferably in separate cases. Clean tools after each use, regularly inspect for wear, use quality coolants, and follow a maintenance schedule. Tool monitoring systems can also help track wear.
What factors should I consider when selecting a cutting tool?
When selecting a cutting tool, consider the material properties, project requirements (e.g., surface finish and tolerances), machining conditions, cost, cutting speed capabilities, and tool coatings. Ensure compatibility with your machine’s power and speed requirements.
How do I know when it’s time to replace a cutting tool?
Signs that it’s time for a replacement include excessive wear, such as flank wear or crater wear, chipping, poor surface finish, or reduced cutting efficiency. Monitoring cutting forces can also help predict when replacement is necessary.
Are premium cutting tools worth the investment?
Premium cutting tools, though more expensive initially, can improve productivity by reducing cycle times and downtime. They may also lower part costs. The decision depends on your specific production needs and machining capabilities.
References
[1] Cutting Tools: Learn the Definition of Cutting Tools with Types [Internet]. Testbook. Available from: https://testbook.com/mechanical-engineering/cutting-tools-definition-properties-and-types
[2] Single Point Cutting Tool- Definition, Nomenclature, and Types [Internet]. Testbook. 2023. Available from: https://testbook.com/mechanical-engineering/single-point-cutting-tool
[3] Double Point Cutting Tool – Examples, Advantages and Disadvantages [Internet]. Minaprem.com. 2018 [cited 2025 Mar 12]. Available from: https://www.minaprem.com/machining/cutter/introduction/double-point-cutting-tool-examples-advantages-and-disadvantages/#google_vignette
[4] Multi-Point Cutting Tool – Examples, Advantages and Disadvantages [Internet]. Minaprem.com. Available from: https://www.minaprem.com/machining/cutter/introduction/multi-point-cutting-tool-examples-advantages-and-disadvantages/
[5] Zhou Y, Xue W. Review of tool condition monitoring methods in milling processes. The International Journal of Advanced Manufacturing Technology. 2018 May;96:2509-23.
[6] ISCAR. Get to Know Cutting Tools: ISCAR’s Reference Guide [Internet]. ISCAR; [cited 2025 Mar 12]. Available from: https://www.iscar.com/Catalogs/publication-2023/english_1/Cutting_tools_user_guide_2023/Cutting_tools_user_guide_2023.pdf
[7] Ramsey M. Price Vs. Cost [Internet]. Aerospace Manufacturing and Design. 2023 [cited 2025 Mar 12]. Available from: https://www.aerospacemanufacturinganddesign.com/article/price-vs-cost-in-cutting-tool-evaluation/
Acquire Premium Quality Cutting Tools at Exceptional Prices with Kota Cutting Tools
Our cutting tools are expertly manufactured and rigorously tested by our technical team to enhance your machining performance and take your business to new heights.