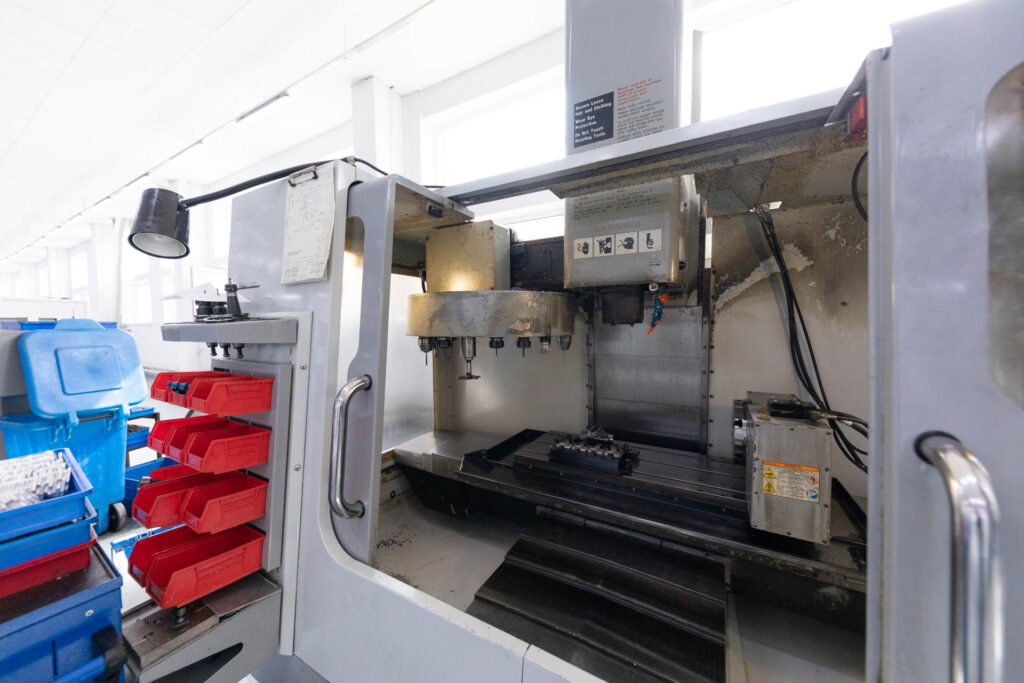
A Comprehensive Guide to CNC Machining Tools
Ever wondered why CNC machines are exceptionally precise and can handle almost anything? You’re not alone!
Sure, the computer brain running the show is a big deal, but the real magic happens with the cutting tools at your disposal. Think of them as the machine’s arsenal – each one a specialized weapon for almost any job imaginable.
Now, let’s machine our way into the types of CNC machining tools, how to correctly select them for your specific operations, and explore the benefits of utilizing first-rate tools for your specific operations.
What are CNC Machining Tools?
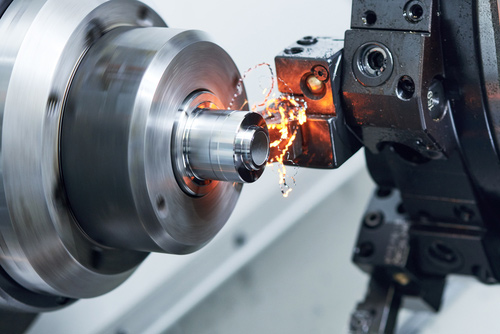
CNC machining tools are automated manufacturing tools that are specialized cutting instruments used in Computer Numerical Control (CNC) machines.
These machines are computer-controlled, allowing for high precision in specified designs and automation in manufacturing processes.
They come in various shapes and sizes, each designed for a specific task, such as drilling, milling, turning, and grinding, to achieve the desired component geometry.
Types of Common CNC Machining Tools
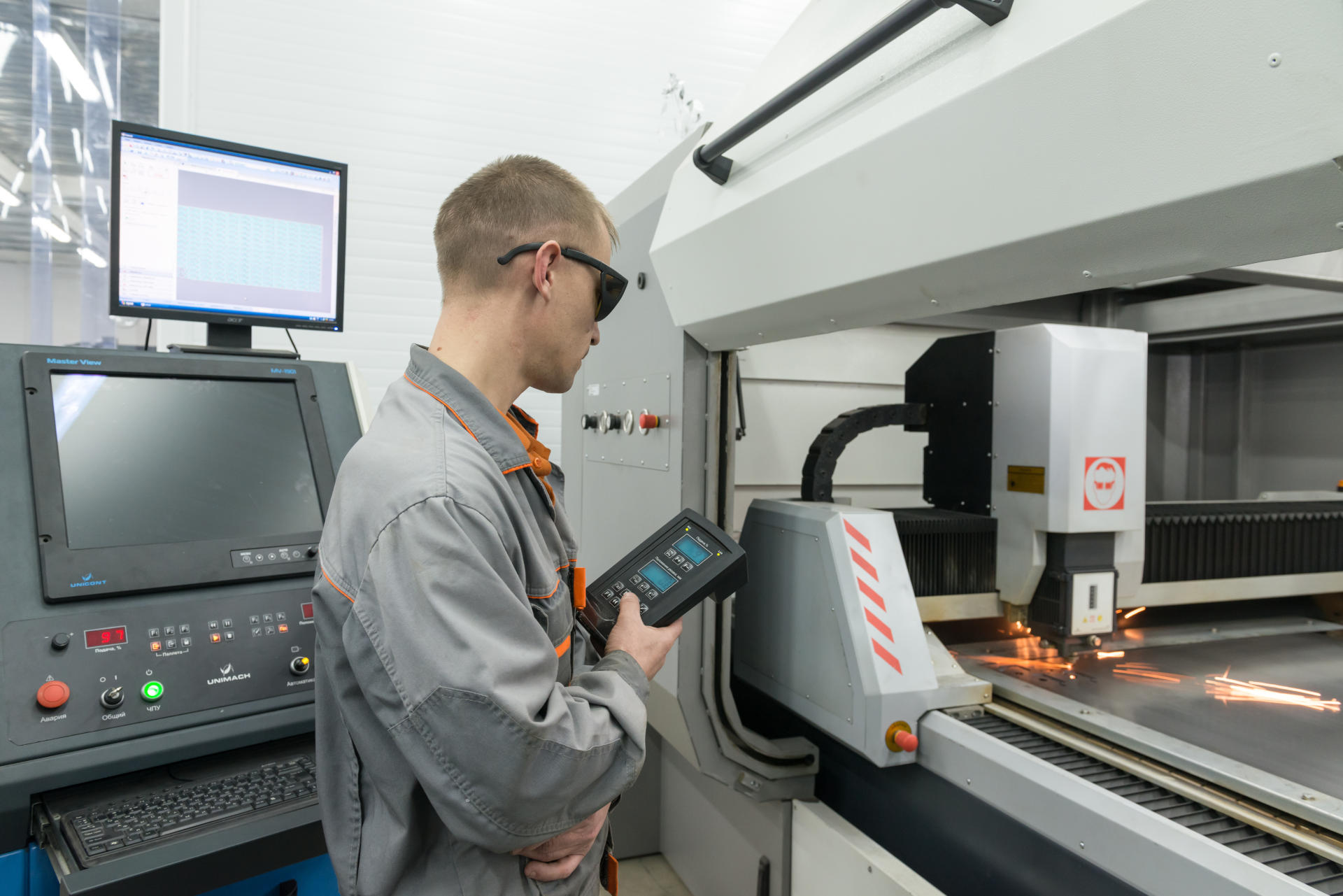
A fundamental step in choosing a CNC machine shop is a thorough understanding of their tools.
Here are some of the most common types of CNC machine tools, along with their primary functions and examples of cutting tools used:
A. Turning Tools
Way back when the Egyptians were building pyramids, turning was already a thing! It’s basically spinning a piece of material and shaving it down with special tools.
CNC turning takes this ancient craft to a whole new level. A super-smart machine called a lathe spins the part super fast, while the tool, guided by a computer, sculpts it into the perfect shape. Think of it like a high-tech potter’s wheel.
Here are some examples of the cool tools used in CNC turning:
1. Facing Tools
Every machinist understands that a perfectly flat end face is essential for a high-quality workpiece. Facing tools specifically create these smooth, accurate end faces.
Built tough and boasting a sharp cutting edge, facing tools ensure your workpieces look professional and fit together flawlessly in assemblies where the end face plays a vital role.
2. Grooving Tools
Not every part is just a simple flat surface! Sometimes, you need to add intricate grooves or recesses for specific functions. That’s where grooving tools come in.
Grooving tools come in two varieties: external and internal. External grooving tools create grooves on the outer surface of a part, while internal grooving tools produce keyways in gears or other specialized internal features.
3. Knurling Tools
Ever wondered how those astonishing, grippy patterns get onto metal tools and parts? These clever little machines, called knurling tools, are the ones that are responsible for creating those unique textures, making things not only look cool but also easier to hold and use [1].
4. Parting Tools
Witnessing a machinist effortlessly separate a finished part from a long piece of metal is truly impressive. This feat is achieved thanks to parting off tools that are razor blades-shaped.
Also known as cutoff tools, these CNC wizards cleanly separate your finished masterpiece from the rest of the material, minimizing the need for extra cleanup.
5. Threading Tools
VOLKEL HSS Round Dies – Metric Fine (MF) metric-fine ISO-thread DIN 13
Threads are everywhere in the world of machines – on nuts, bolts, and countless other parts. Creating perfectly formed threads is crucial for everything to fit and function smoothly.
Similar to grooving tools, they also exist in two types: external and internal. A key tool for creating these internal threads is the machine tap.
Learn more about our selection of machine taps here!
B. Milling Tools
Milling tools, often called cutters, shape workpieces by carefully removing material, much like miniature sculptors. These versatile tools find applications across industries, from crafting intricate wooden pieces to shaping complex metal parts like gears.
With their multi-angled capabilities, these machines streamline the manufacturing process for intricate wood, metal, and plastic parts [2].
1. Boring Tools
Contrary to their name, boring tools are anything but boring. In fact, they delicately enlarge existing holes to achieve perfect, customized diameters.
Think of it like this: the boring bar is like a versatile artist, equipped with a ‘boring head’ that can be outfitted with different cutting inserts to tackle any material and achieve the desired finish.
But the process doesn’t stop there. Other tools like reamers step in to fine-tune the hole size to absolute perfection, while specialized drill bits lay the initial groundwork for this precise sculpting process.
2. End Mills
KCT HSS-CO8 2 FLUTE & 4 FLUTE END MILLS
A traditional end mill operates much like a spinning pencil, cutting primarily with its sharp tip. In contrast, a face mill resembles a spinning wheel, utilizing its broad, flat face for cutting.
This unique design distributes the cutting force across multiple edges, resulting in a smooth, even cut and maximizing tool life.
3. Reamers
Just as a sculptor refines their work with delicate chisels, the reamer is the master of precision in the CNC machining world. While boring tools create the initial shape, the reamer takes over, meticulously honing pre-drilled holes to achieve the exact, flawless diameters demanded by the design.
Think of it as the finishing touch, bridging the gap between a hole that’s ‘almost right’ and one that’s absolutely perfect. In the realm of CNC machining, where even the slightest imperfection can have significant consequences, the reamer’s role in ensuring unparalleled accuracy is truly invaluable.
C. Drilling Tools
Machinists rely on drilling tools, often called drill bits, to create precise holes in their workpieces. Whether used with manual twist drills or sophisticated CNC mills, these versatile tools utilize spiraling flutes and tapered cutting points to bore through various materials efficiently.
Here are some examples of common drilling tools:
1. Centre Drills
KCT SOLID CARBIDE Centre drills – MM & Inch
Before unleashing larger drill bits on a workpiece, machinists employ a crucial first step: using a center drill. This specialized tool creates a small, perfectly aligned starting point – a precisely located and centered indentation.
The initial mark is an unwavering guide for subsequent drilling operations, ensuring accuracy and preventing the more significant drill bit from wandering or drifting off course. By establishing this precise foundation, the center drill significantly enhances the overall quality and precision of the finished hole.
2. Ejector Drills
After the center drill establishes the perfect starting point, the ejector drill takes center stage. These specialized drills, designed for precision and efficiency, seamlessly enlarge the initial indentation into a larger, deeper hole.
Ejector drills feature a unique design that facilitates the removal of chips and debris during the drilling process, preventing clogging and ensuring a smoother cutting action.
3. Drill Bits
CNC drill bits are a far cry from the basic bits you might find in your home drill. Similar to boring tools, these drill bits are tiny, specialized sculptors that meticulously carve perfect holes into your workpiece with a whole new level of precision.
Each bit is a masterpiece of engineering, crafted in various sizes and with unique coatings to conquer any material and depth. In the CNC world, drilling isn’t just about making a hole; but a perfectly round, precisely sized, and exactly where it needs to be.
D. Grinding Tools
CNC machines, armed with high-precision abrasive wheels, are masters of surface finishing. This subtractive grinding process surpasses the accuracy of any 3D printing method, achieving an almost flawless surface.
In fact, these machines can reduce imperfections to tolerances so minuscule they’re barely imaginable – as small as 1/10th the width of a human hair! Some of these tools include:
1. Grinding Wheels
Grinding wheels are the beating heart of any precision grinding operation. These specialized tools are not mere spinning disks but meticulously engineered composites designed to shape and refine materials with unparalleled accuracy.
2. Superabrasive Wheels
When precision demands exceed the capabilities of conventional grinding wheels, superabrasive wheels step onto the stage. Crafted from materials like diamond and cubic boron nitride (CBN), these extraordinary tools boast exceptional hardness, wear resistance, and cutting ability.
E. Cutting Tools
CNC machines truly shine when precision and efficiency are paramount, particularly for intricate cutting tasks:
1. Gear Cutters
Gear cutters, as their name implies, are specialized tools designed to bring gear manufacturing to life. These ingenious tools possess the versatility to fabricate a wide array of gear types, each with its unique purpose.
2. Saws
CNC sawing machines are indispensable for precise and efficient material separation. These tools include band saws, circular saws, abrasive waterjet cutting, and laser cutting.
Premium Quality Cutting Tools at Competitive Prices
Our cutting tools are expertly manufactured and rigorously tested to enhance machining performance and operational savings.
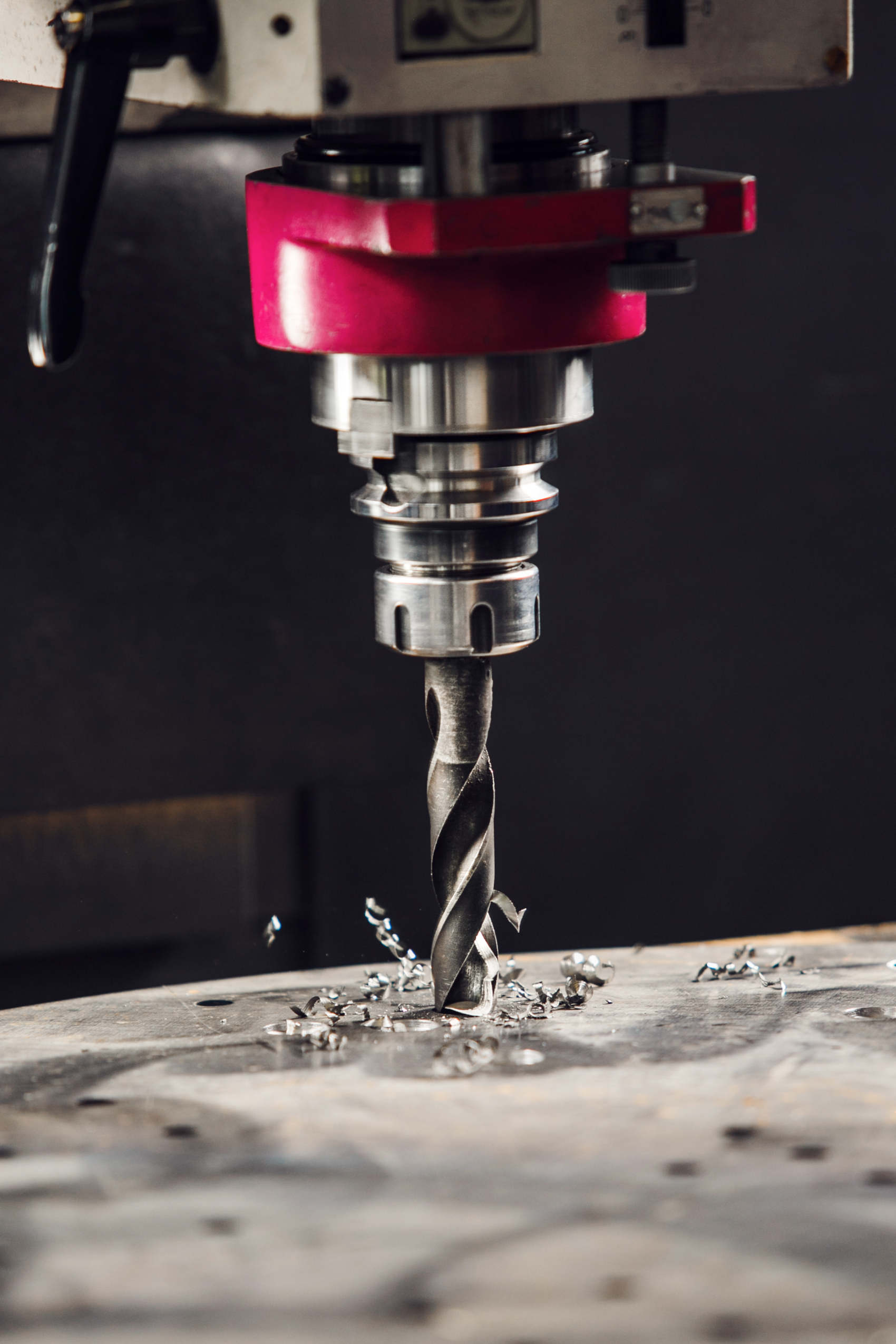
How to Select CNC Tooling
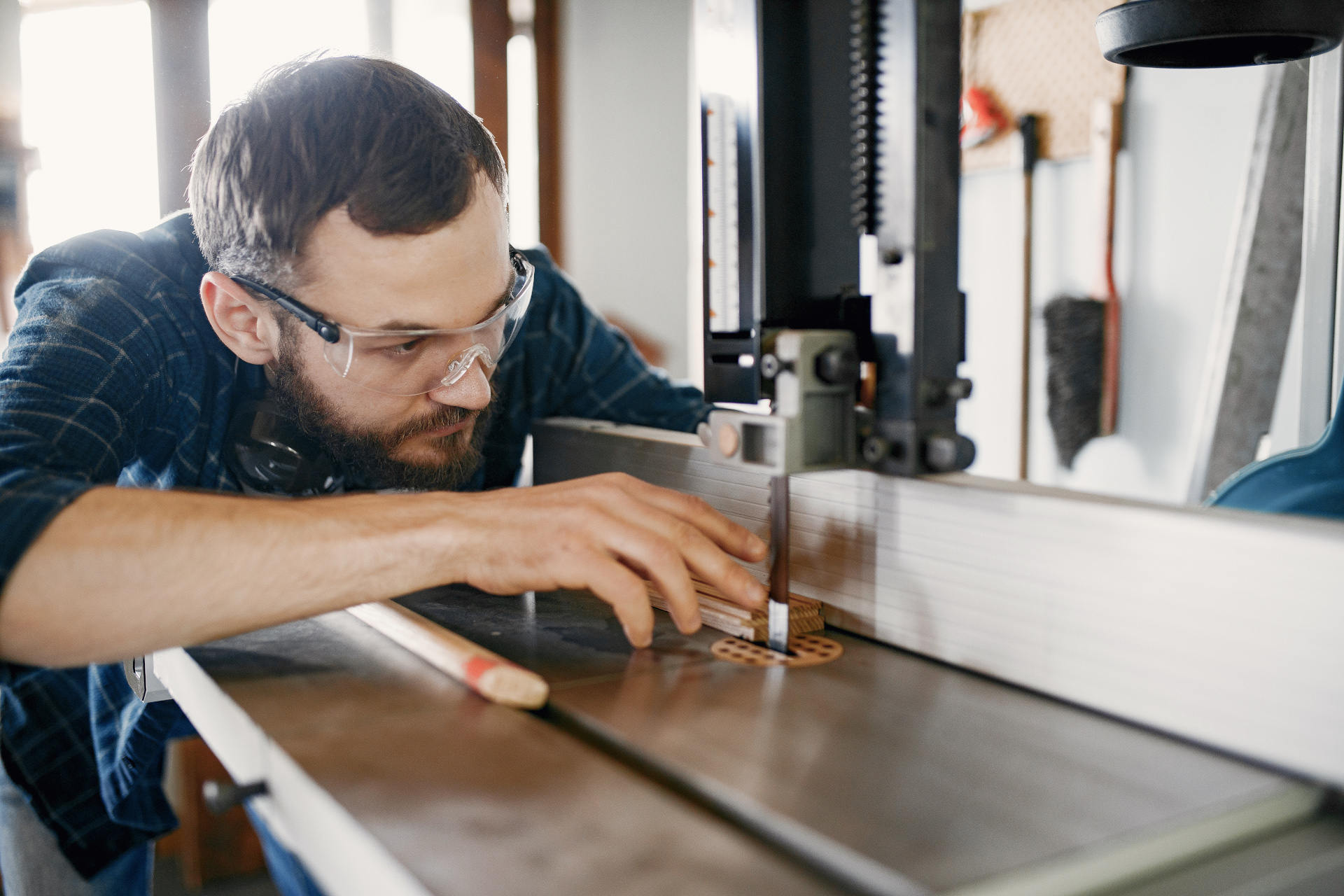
Choosing the right CNC tooling is crucial for achieving optimal machining performance, maximizing productivity, and minimizing costs. Here’s a breakdown of key factors to consider:
1. Material Compatibility
Machining different materials demands different tools – just like using the right screwdriver for the right screw. The workpiece material significantly influences the selection of appropriate cutting tools.
For instance, more rigid materials necessitate the use of tougher tools, such as carbide or ceramic inserts.
To keep things efficient and cost-effective, you’ll need to rely on standardized tooling whenever possible.
2. Application to Production
The intricate dance of machining demands a deep understanding of its nuances. Each operation, whether the forceful bite of milling, the precise plunge of drilling, or the elegant sweep of turning, necessitates a unique set of tools meticulously crafted with specific geometries and robust coatings.
These tools, in turn, are intricately intertwined with the cutting conditions – the speed at which they cut, the rate at which they advance, and the depth they penetrate.
3. Durability of CNC Tools
Durability is the testament of quality that transcends to longevity; and just like your CNC tools, it must have the unwavering ability to withstand the relentless assault of time, wear and tear, and other unpredictable forces of the environment [3].
Whether it’s a timeworn tool’s steadfast resilience or a high-tech gadget’s unwavering performance, durability can be further enhanced if coated with the right surface finish. This helps improve the tool’s wear, heat, and friction resistance.
Benefits of Using High-Quality CNC Tools
When it comes to CNC machining, the quality of your tools can significantly impact the accuracy, efficiency, and overall success of your operations. Investing in high-quality CNC tools offers a range of benefits that can lead to improved productivity, reduced costs, and enhanced product quality. This helps you ensure:
1. Enhanced Precision and Accuracy
- Tight tolerances: High-quality tools maintain precise dimensions and tight tolerances, ensuring your parts meet exact specifications.
- Reduced errors: The consistent performance of high-quality tools minimizes the risk of errors, such as tool breakage or chatter, which can lead to costly rework or scrapped parts [4].
2. Increased Efficiency and Productivity
- Faster cutting speeds: High-quality tools are often made from premium materials and feature advanced geometries, allowing for faster cutting speeds and increased material removal rates.
- Longer tool life: Durable tools can withstand the rigors of CNC machining for extended periods, reducing the frequency of tool changes and minimizing downtime.
- Improved surface finish: High-quality tools produce smoother and more consistent surface finishes, reducing the need for additional finishing processes.
3. Reduced Downtime and Maintenance Cost
- Lower maintenance costs: Durable tools require less frequent maintenance and replacement, leading to lower overall maintenance costs.
- Reduced scrap rates: The precision and reliability of high-quality tools minimize the risk of producing defective parts, reducing scrap rates and associated costs.
- Increased machine utilization: Increased machine utilization: Faster cutting speeds and reduced downtime due to tool changes maximize machine utilization, increasing production output.
4. Other Benefits
- Increased safety: High-quality tools are designed with safety in mind, reducing the risk of accidents or injuries.
- Improved process control: The consistent performance of high-quality tools makes it easier to control and optimize the CNC machining process.
- Enhanced competitiveness: By producing high-quality parts efficiently, you can gain a competitive edge in the market.
Improve Your Bottom Line with Efficient CNC Solutions!
Unlocking the full potential of your CNC machining starts with selecting the right tools.
Elevate your CNC machining with Kota Cutting Tools today and experience the difference precision makes.
Explore our premium selection and contact us today to get a free consultation!
References
[1] Olejnik A, Kapitanov A, Alexandrov I, Tatarkanov A. Designing a tool for cold knurling of fins. Istraživanja i Projektovanja za Privredu. 2020;18(3):305-12. doi:10.5937/jaes18-25786.
[2] WAYKEN Rapid Manufacturing. Milling Cutter Tools Explained – Types and Selection Guide [Internet]. WAYKEN Rapid Manufacturing; 2025. [cited 2023 Oct 26]. Available from: https://waykenrm.com/blogs/milling-cutter-tools/
[3] CNC Machining Material Selection Guide [Internet]. American Micro Industries. [cited 2024 November 26]. Available from: https://www.americanmicroinc.com/resources/cnc-machining-material-guide/
[4] Pajaziti A, Tafilaj O, Gjelaj A, Berisha B. Optimization of Toolpath Planning and CNC Machine Performance in Time-Efficient Machining. Machines. 2025; 13(1):65. https://doi.org/10.3390/machines13010065
Acquire Premium Quality Cutting Tools at Exceptional Prices with Kota Cutting Tools
Our cutting tools are expertly manufactured and rigorously tested by our technical team to enhance your machining performance and take your business to new heights.